Repurposing Food Scraps
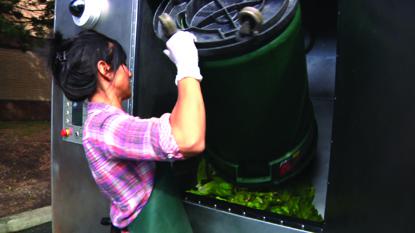
In April 2010, the cofounders of WISErg Corporation called PCC Natural Markets (PCC), a Seattle-based natural foods co-op, to introduce their idea for converting food scraps into a new product. Their business proposition was simple: with WISErg’s new process, a grocery retailer could avoid the financial and environmental costs of transporting food scraps offsite and create a new source of revenue by capturing and repurposing the nutrients in those scraps.
WISErg, a local startup, needed a partner willing to let them study—hands-on and on a daily basis—the origin, volume, composition, and disposal of food scraps within a grocery operation. WISErg would gain knowledge and experience from testing their idea in a real-world setting. PCC would have the opportunity to be part of a new solution to the old problem of responsible organic material disposal.
The PCC store in Issaquah, Wash., was chosen for WISErg’s living laboratory. Three years later, both organizations had gotten what they wanted—and a great deal more.
Food waste costs
According to the Environmental Protection Agency, food waste generated in the U.S. topped 36 million tons in 2011. Consumers, food establishments, and even sustainably operated grocery retailers like PCC contribute to food waste and the resulting negative environmental impact and nutrient loss.
PCC donates past-sell-date food and produce culls to local nonprofits and farmers, but most food scraps generated by the fresh departments of the co-op’s nine stores are trucked to a commercial composting facility. This disposal option is convenient, but significant costs are involved. A considerable volume of greenhouse gases is generated from the transport of food scraps to the facility. An estimated 80 percent of nutrient content is lost during the composting process. Compost hauling fees average in the thousands of dollars per store annually.
The WISErg zero-waste nutrient-recovery system
The WISErg system processes food scraps onsite and repurposes the nutrients in them so there is virtually no waste and only minimal environmental impact.
The heart of the system is the Harvester. On the outside of this silver box are a control panel, camera, and door. The password-protected door opens to a chute into which food scraps are dumped. WISErg-trained store employees load the Harvester with food scraps, typically using five-gallon buckets. The source of each load—meat and seafood, produce, deli, etc.—is keyed into the control panel. The date, time, and weight of each load are recorded automatically, providing valuable data for later analysis by WISErg and PCC.
A grinder installed below the chute chews up food waste of all kinds, as well as acceptable compostables such as food-soiled paper products. After loading, employees shut the door and begin a two- to three-minute grinding cycle. If at any time staff are concerned about how the Harvester is operating, they can push a halt button on the control panel, which immediately shuts down the system. An automatic diagnostic system signals WISErg, and a WISErg employee responds within 30 minutes to either remotely reset the system or arrange for an onsite visit.
Following the grinding process, the resulting slurry is pumped into an adjacent 3,500-gallon biology tank. Within hours, WISErg’s proprietary mix of single-cell organisms devours the slurry, converting it into a biomass that acts to stabilize the nutrients. Sensors notify WISErg when the biomass is ready for pickup. Their truck arrives, and in less than 10 minutes the tank is pumped out for transport offsite for further refinement.
From biomass to liquid gold
At a nearby WISErg facility, the biomass is held in a transition tank for 24 hours to ensure complete conversion. Any nonorganic solids are filtered out at this point. The filtered product is moved into an adjacent processing tank where a second feeding frenzy, involving even more aggressive microorganisms, consumes the remaining nutrients. Separation of the liquid from the biomass is done with a centrifuge; the nutrients are then extracted from the biomass using food-grade processes and remixed with a portion of the original liquid. The final step is a sterilization process that destroys any pathogens that may remain in the product that will be shipped to market.
WISErg analyzes and balances the liquid to meet desired levels of proteins, amino acids, fatty acids, antioxidants, and other compounds. The final result is a fertilizer that not only is effective, but also is certified for use on organic crop production by the Washington State Department of Agriculture. The fertilizer, branded as Wiserganic, is sold at all PCC locations as well as to local farms.
The WISErg system vs. anaerobic digestion
WISErg initially considered developing a system based on anaerobic digestion, a process familiar in rural settings that converts animal and plant waste into biogas. Anaerobic digestion is a catabolic process that breaks down complex molecules into simpler ones, in the absence of oxygen. It releases energy, and the nutrients in the organic matter are lost as a result.
WISErg decided to pursue a different process that would retain the nutrients in food scraps and be more suitable for an urban environment where limited space, noise, and odor control are important considerations.
The WISErg system is primarily an anabolic process that seeks to maintain the complex molecules of organic material in their complex state. In contrast to anaerobic digestion, which decomposes organic material to create energy, the WISErg approach grows a nutrient-rich organic material. Oxygen is necessary to keep WISErg’s organisms healthy—and also well-behaved. Not unlike kids, these organisms crave sugar and carbs. If they become too excited, sensors reduce oxygen flow in the tank accordingly. Similarly, proteins require more oxygen to stimulate feeding. The tank’s ecosystem requires little more than maintaining optimum oxygen levels and a moderate temperature for the organisms to eat and stay healthy. Both conditions are monitored and controlled remotely by WISErg.
The business case for the WISErg system
The WISErg system can process 4,000 pounds of food scraps daily, making it adequate for grocery operations the size of newer PCC stores (up to 25,000 square feet) and for shared use by smaller food establishments. The system is quiet and produces no odor, and its two-part configuration can be modified for a variety of locations. WISErg systems now operate at two PCC locations; three more are planned within the next year.
The WISErg system provides PCC with more than a better solution for food scrap disposal. “Dumpster data”—the information each Harvester records—provide PCC details about the waste stream at its Harvester stores that was unknown before. Real-time reports for source and weight of food-based waste are expected to give PCC management a tool for better control over its waste production by store and by department, as well as visibility in labor and training opportunities. It is too soon to know the full impact of the WISErg system on reducing shrink, but early indications are that this new information could lead to significantly tighter loss control.
PCC estimates a four- to five-year return on investment for each Harvester system. On the plus side are reduced fees and a smaller carbon footprint from not hauling food scraps offsite, as well as anticipated savings from reduced shrink. PCC shoppers also like being able to buy high-quality fertilizer made only from the same high-quality food they buy at PCC. For sale since May 2012, unit sales of Wiserganic have increased more than 250 percent (third quarter 2013 vs. 2012).
PCC hopes the WISErg system soon will be welcomed by other food establishments and Wiserganic will gain popularity among gardeners and farmers across the country. It all will have started with a phone call, and the mutually beneficial partnership of a natural food co-op and a like-minded local startup.
For more information about the WISErg system, contact Larry LeSueur,
co-founder and CEO: Harvester@wiserg.com, 800-592-2511, or
www.wiserg.com.